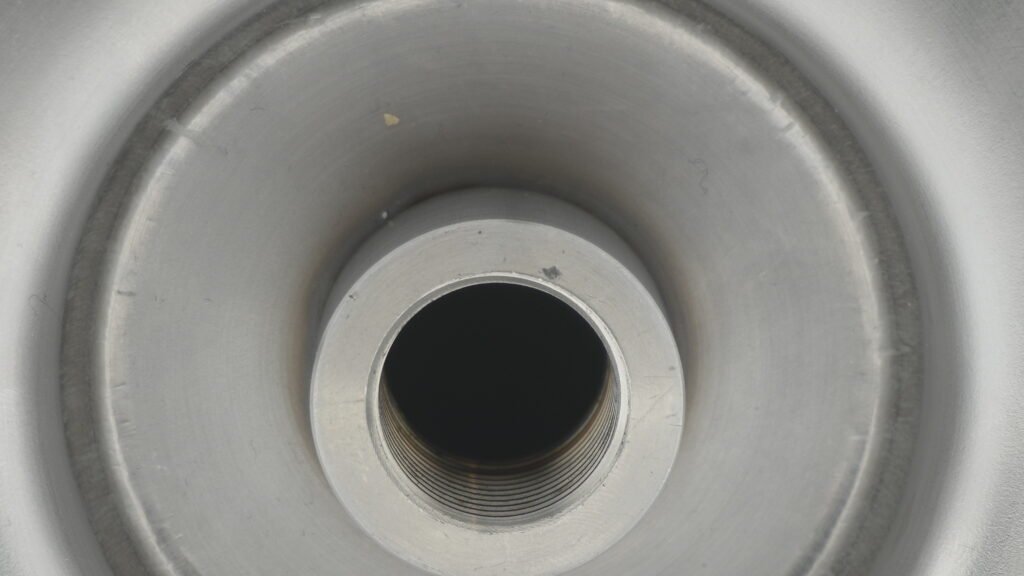
Understanding Air Spring Varieties
Air springs, also known as pneumatic actuators, come in various configurations to accommodate different industrial and automotive applications. Selecting the appropriate air spring type ensures optimal performance in vibration isolation, load support, and actuation systems. The right selection depends on factors such as load-bearing capacity, stroke length, operating pressure, and durability in extreme environments.
These air springs are built with reinforced elastomers and robust metallic components to ensure long-lasting performance. Each type has unique characteristics that make it suitable for specific applications. By understanding their capabilities, industries can choose the most efficient and cost-effective solutions. Properly selected air springs improve equipment longevity, reduce maintenance costs, and enhance operational stability. With their wide range of sizes and pressure capabilities, air springs are among the most versatile mechanical components in modern engineering.
Single Convolute Air Springs
Single convolute air springs feature a single flexible chamber that expands and contracts under compressed air pressure. They are widely used in precision machinery, conveyor systems, and vibration control platforms. Their compact design allows for installation in confined spaces while maintaining excellent load-bearing capabilities.
These air springs generally operate under pressures ranging from 3 bar to 10 bar, depending on the specific model. Their load-bearing capacity varies between 2 kN and 40 kN, making them ideal for light to medium-duty applications. Single convolute air springs also have minimal hysteresis loss, ensuring efficient energy transfer. The flexibility of these springs allows for slight misalignment compensation, reducing the need for additional guiding mechanisms. The elastomer materials used in these springs include natural rubber, EPDM, and NBR, ensuring compatibility with various environmental conditions.
Double Convolute Air Springs
For applications requiring increased stroke and load-bearing capacity, double convolute air springs are the preferred choice. These air springs provide better stability and versatility, making them ideal for heavy-duty vehicles, press machines, and automated manufacturing lines.
Double convolute air springs feature two flexible chambers that expand and contract under pressure, allowing for greater height adjustability between 65 mm and 285 mm. Their higher force output ranges from 5 kN to 100 kN, accommodating more demanding applications. These springs can withstand extreme temperature variations, from -40°C to +115°C, ensuring reliable performance in harsh environments. Additionally, they provide excellent lateral stability, reducing vibrations and preventing mechanical stress in dynamic systems. The inclusion of galvanized or stainless steel bead plates further enhances their resistance to corrosion and mechanical wear.
Triple Convolute Air Springs
When maximum stroke and load capacity are necessary, triple convolute air springs offer exceptional performance. These springs excel in railway suspension systems, heavy machinery supports, and shock-absorption platforms.
Triple convolute air springs provide an extended vertical stroke range of up to 375 mm, making them highly versatile. They have exceptional load distribution capabilities, supporting up to 300 kN per unit. Their low natural frequency reduces resonance below 1.5 Hz, making them highly effective in vibration isolation applications. These air springs are typically made from high-strength elastomers such as EPDM and NBR, offering resistance to oils, chemicals, and extreme weather conditions. They are also tested to endure millions of compression cycles, making them a long-term investment for high-performance industrial systems.
Industry-Specific Applications
Automotive and Transportation
Air springs play a crucial role in commercial vehicle suspensions, bus chassis systems, and trailer load leveling. Their ability to provide consistent ride height and reduced road vibrations makes them indispensable in modern transportation.
In commercial vehicles, air springs operate under pressures between 4 bar and 9 bar, ensuring smooth suspension performance. They also improve driver comfort by reducing harsh road impacts. Air springs used in transportation are built with weather-resistant materials, ensuring durability in extreme heat, cold, and humidity. Advanced models include integrated height control valves, automatically adjusting pressure to maintain an optimal ride height under varying load conditions.
Industrial Machinery
Many manufacturing processes rely on pneumatic vibration isolators to enhance precision and protect sensitive equipment. Press brakes, injection molding machines, and conveyors benefit significantly from air spring technology.
Air springs in industrial applications operate at pressures ranging from 3 bar to 12 bar, ensuring precise and consistent actuation. They can withstand continuous compression cycles exceeding 2 million operations, making them low-maintenance solutions. These air springs also feature adjustable stroke lengths up to 450 mm, allowing custom configurations to meet specific industrial needs. Galvanized and stainless steel bead plates further enhance their resistance to harsh factory environments, extending operational longevity.
Heavy-Duty Equipment
Construction vehicles, mining machinery, and lifting platforms depend on robust air spring solutions for load balancing, impact absorption, and shock mitigation.
Heavy-duty air springs have compression capabilities exceeding 10,000 kg per unit, making them ideal for extreme load-bearing applications. Their reinforced elastomers offer superior resistance to abrasion, oil exposure, and mechanical stress. Heavy-duty models also feature custom mounting configurations, including bolt-through and threaded stud options, providing installation flexibility across different machinery designs. These air springs undergo intensive fatigue testing, ensuring consistent performance over years of heavy operation.
Medical and Laboratory Equipment
For applications requiring zero vibration, such as MRI machines and high-precision measuring instruments, air springs provide the ultimate level of isolation.
Medical-grade air springs are designed with ultra-low natural frequencies, absorbing over 99% of unwanted vibrations. Their elastomer compounds are non-reactive, preventing contamination in sterile environments. These air springs also feature anti-static properties, eliminating risks in electronic-sensitive applications. Compact and maintenance-free, these air springs provide a cost-effective alternative to conventional hydraulic dampening systems.
Choosing the Right Air Spring
Factors to Consider
- Load Capacity – Ensure the air spring can handle the required weight, typically between 2 kN and 300 kN.
- Operating Pressure – Match the air pressure requirements for optimal functionality, from 3 bar to 12 bar.
- Stroke Length – Consider the required vertical movement range, usually 50 mm to 450 mm.
- Material Composition – Select materials resistant to chemicals, oils, or extreme temperatures, such as NR, EPDM, or NBR.
By understanding the different air spring types and their specific applications, industries can select the best solution to improve efficiency, safety, and durability. Whether for transportation, industrial automation, or specialized applications, air springs remain an essential component in modern engineering. Incorporating high-quality elastomers, robust metal fittings, and advanced design techniques ensures long-lasting performance and optimal mechanical efficiency.