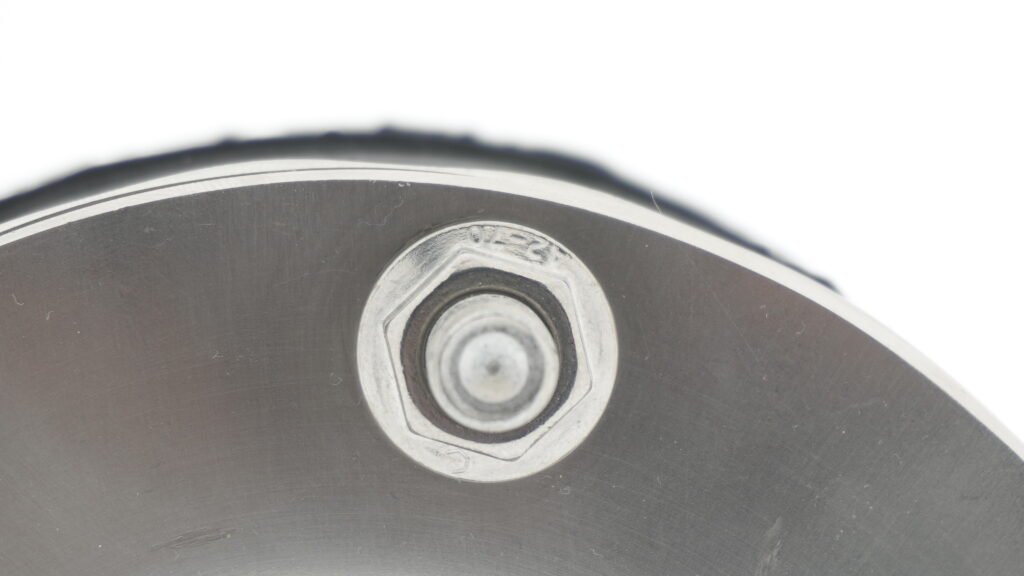
The development of air bellows has transformed multiple industries by improving vibration isolation, actuation capabilities, and shock absorption. These flexible components have evolved significantly, adapting to the growing demands of industrial machinery, transportation, and pneumatic systems. By understanding the history and technological advancements of air bellows, we gain valuable insight into their increasing role in modern engineering. Over the years, the structural composition, operational efficiency, and durability of air bellows have undergone significant improvements, making them indispensable in various high-performance applications.
The Early Development of Air Bellows
The origins of air bellows date back to the early 20th century, when industries sought better suspension systems for vehicles and machinery. Traditional coil springs and hydraulic dampers provided limited shock absorption and wore out over time. This need led to the introduction of rubberized air springs, offering a more adaptable and durable solution for mechanical vibration control. Early models featured single-layer rubber structures reinforced with woven fabric, which allowed elastic deformation under applied loads. These rudimentary designs were later improved by introducing multi-layered reinforcement, allowing for better pressure containment and extended lifespan.
Key Innovations in Early Designs
- Rubber-reinforced bellows were introduced for improved flexibility and shock resistance.
- Compressed air was adopted as an elastic medium, allowing for adjustable load distribution.
- Early applications included railway suspension systems, automotive shock absorbers, and industrial vibration dampers.
- Introduction of metallic bead rings for secure mounting and enhanced durability.
The Evolution of Air Bellows in Industrial Applications
With rapid industrialization, air bellows became widely used in manufacturing, automotive suspension, and pneumatic actuation. Advances in rubber chemistry, reinforcement materials, and sealing technologies enhanced their durability and efficiency. The addition of elastomer compounds enabled air bellows to function under extreme environmental conditions, including high temperatures, chemical exposure, and mechanical fatigue.
Advancements in Material Technology
- Natural rubber (NR/SBR): Offers high elasticity, impact resistance, and mechanical flexibility.
- Nitrile rubber (NBR): Provides enhanced oil and fuel resistance, making it ideal for automotive and hydraulic applications.
- Chlorobutyl rubber (CIIR): Delivers superior acid and chemical resistance, ensuring long-term performance in harsh environments.
- Ethylene Propylene Diene Monomer (EPDM): Excels in ozone and UV resistance, extending service life in outdoor applications.
- Four-ply construction enables higher pressure applications up to 12 bar (standard is 8 bar), providing increased load-handling capacity.
- Integration of steel cord reinforcement improves structural integrity, reducing deformation under heavy loads.
Industrial Applications of Air Bellows
Modern air bellows serve multiple industries by providing precision force control, shock absorption, and vibration isolation. These systems enhance operational efficiency by reducing mechanical wear, improving stability, and adapting to variable loads.
Manufacturing & Automation
- Actuators in robotic machinery enable precise motion control.
- Press systems requiring force modulation benefit from adjustable air bellows.
- Heavy-duty lifting mechanisms rely on pneumatic pressure variation to achieve smooth elevation.
- Force capacities range from 0.5 kN to 450 kN per unit, ensuring compatibility with diverse industrial applications.
- Axial stroke lengths from 50 mm to 375 mm provide versatile positioning capabilities.
- Fatigue-resistant rubber compounds extend service life, reducing downtime and maintenance costs.
Transportation & Automotive
- Suspension systems in trucks, buses, and railways enhance riding comfort and stability.
- Load-balancing systems for heavy-duty vehicles distribute axial loads evenly, improving fuel efficiency.
- Noise and vibration isolation in vehicle cabins reduces structural fatigue and operator discomfort.
- Operating temperature range: -40°C to +115°C, ensuring durability in extreme climates.
- Bead rings or crimped seals improve air retention, minimizing pressure loss over extended usage.
- Advanced elastomer coatings prevent chemical degradation, extending operational lifespan in industrial fleets.
Construction & Heavy Equipment
- Shock absorbers in off-road and mining equipment protect against harsh terrain-induced vibrations.
- Load equalization in construction vehicles ensures structural balance under variable loads.
- Structural support in bridge bearings mitigates stress accumulation, prolonging infrastructure stability.
- Compact installation height enables integration in space-restricted areas.
- Pneumatic leveling solutions facilitate load balancing on uneven terrain.
Future Trends in Air Bellows Technology
With advancements in material science, automation, and predictive maintenance, future air bellows will focus on:
- Smart monitoring systems providing real-time diagnostics for predictive failure analysis.
- Enhanced elastomer compounds designed for abrasion and wear resistance.
- Eco-friendly manufacturing processes, reducing carbon footprint and industrial waste.
- Stronger nanocomposite rubber materials for improved durability under high-pressure applications.
- IoT-integrated sensors optimizing performance tracking, ensuring early maintenance intervention.
- Hybrid pneumatic-electric actuation systems, combining air compression efficiency with digital precision control.
The history and evolution of air bellows highlight their growing importance in industrial applications. They have evolved from basic shock absorbers to high-performance pneumatic components, supporting heavy loads, reducing mechanical wear, and enhancing suspension stability. Their ability to absorb vibrations, actuate machinery, and improve transportation efficiency makes them essential in engineering and manufacturing. As technology advances, air bellows will continue to evolve, offering greater efficiency, durability, and adaptability.