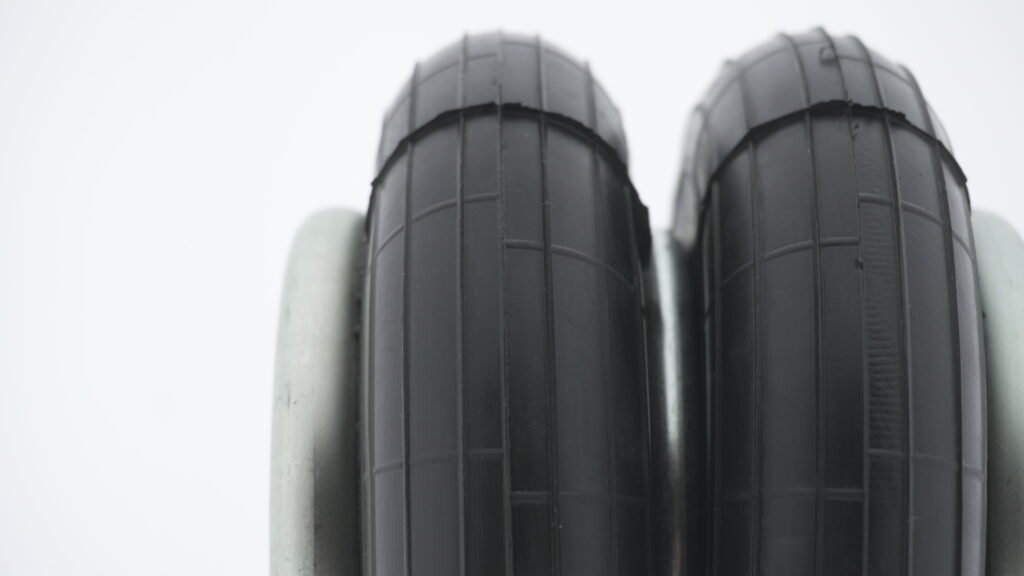
Innovations in Air Bellow Materials
In the industrial sector, air bellows are essential components that provide high-performance vibration isolation, load leveling, and shock absorption. Recent advancements in elastomer technology and reinforced composite materials have significantly enhanced the durability, efficiency, and resistance of air springs in demanding environments. The integration of new materials enables manufacturers to design air springs that withstand higher pressures and longer operational lifespans. With enhanced fatigue resistance, these innovations allow air springs to function more reliably under extreme conditions. The importance of weight reduction and sustainability in modern engineering has led to the development of lighter yet stronger air springs. These changes contribute to greater fuel efficiency and lower emissions, making them ideal for automotive and industrial applications. Engineers can now select tailored solutions to meet specific operational needs, optimizing performance and longevity.
The Evolution of Elastomers in Air Bellows
The core of an air bellow consists of high-strength elastomer compounds, each tailored for specific applications. These elastomers determine resistance levels to heat, chemicals, and wear, ensuring that air springs last longer. Natural Rubber (NR/SBR) is commonly used for general-purpose applications, offering high flexibility and strong dynamic capabilities. For applications requiring acid resistance, Chlorobutyl (CIIR) is an excellent choice, extending durability in corrosive environments. Nitrile Rubber (NBR) is used for oil and fuel resistance, making it an industry standard for hydraulic systems. Ethylene Propylene Diene Monomer (EPDM) is ideal for outdoor applications, as it provides superior weather resistance and thermal stability. Chloroprene (CR) balances chemical and oil resistance, making it a reliable option for various industrial uses. Selecting the right elastomer ensures optimal performance, extending the lifespan of air bellows in diverse environments.
Strengthening Metal Components in Air Springs
To ensure structural integrity, air bellows incorporate metallic end closures made of various materials. These metallic components play a crucial role in maintaining pressure stability and ensuring attachment strength. Electro-Galvanized Steel is widely used for general applications, offering a cost-effective solution with good corrosion resistance. For environments exposed to chemicals and moisture, Stainless Steel AISI-304 provides higher durability. Applications requiring exceptional corrosion resistance, such as marine industries, benefit from Stainless Steel AISI-316L. Advanced coating techniques, such as powder coatings and anodization, further extend the lifespan of metal components. Manufacturers are also developing lightweight aluminum alternatives, ensuring weight reduction without sacrificing strength. These metal enhancements help air bellows maintain durability, support heavy loads, and enhance overall efficiency across various industries.
Advanced Fabric Reinforcement in Air Bellows
Modern air springs are reinforced with multi-ply fabric layers, improving burst resistance and pressure endurance. The incorporation of high-strength fibers enhances structural stability, preventing premature failures in high-pressure applications. Two-Ply Construction is common in low to medium pressure applications, ensuring sufficient flexibility and load-bearing capacity. Four-Ply Construction offers higher reinforcement, allowing air springs to handle increased loads. Kevlar-Reinforced Layers provide exceptional tensile strength, making them suitable for extreme conditions in aerospace and heavy-duty industries. Advances in textile coatings and heat-resistant fibers further improve longevity and reliability. These reinforcement methods ensure long-term durability, making air bellows more reliable under challenging industrial conditions.
Pressure and Load-Bearing Enhancements
The evolution of air bellows materials has led to increased pressure ratings and load-bearing capabilities. These advancements ensure optimal functionality, reducing mechanical stress and deformation. Standard air bellows are designed to handle pressures up to 8 bar, making them ideal for most industrial applications. For heavier-duty applications, manufacturers have developed high-pressure variants capable of withstanding up to 12 bar. The introduction of reinforced composite layers allows for higher force output, improving performance and reliability. Load-bearing capacities range from 0.5 kN to 450 kN, enabling greater flexibility across industries. Engineers can select specific configurations tailored for individual operational needs. These improvements contribute to longer service life, better efficiency, and enhanced performance in high-demand sectors.
Energy Efficiency and Sustainability
Modern air bellows contribute to energy savings and environmental sustainability. The integration of eco-friendly elastomers reduces carbon footprints while maintaining high-performance standards. Lower compressed air consumption ensures reduced operating costs, benefiting industries focusing on energy efficiency. Materials designed for minimal wear extend service life, reducing replacement frequency. The use of recyclable rubber compounds allows for environmentally responsible disposal. Industries are shifting towards sustainable materials, reducing waste and environmental impact. Lightweight air bellows improve fuel efficiency, making them ideal for automotive applications. These innovations support global sustainability efforts, ensuring resource conservation and responsible manufacturing.
Application-Specific Design Innovations
To meet the demands of various industries, air bellow manufacturers have introduced specialized design features. In automotive and heavy-duty vehicles, load-leveling air springs maintain optimal ride height and stability. Shock-absorbing air bellows improve passenger comfort by reducing vibrations. In industrial machinery, vibration isolation bellows protect sensitive equipment from excessive mechanical stress. Precision motion actuators ensure uniform force distribution, improving machine efficiency. Aerospace applications utilize lightweight, high-strength composites, reducing weight while maintaining durability. These specialized air bellows enhance performance across diverse applications.
Customization and Adaptability
Modern air bellows are now available in customized configurations, catering to specific engineering requirements. Variable convolution designs allow for different motion profiles, making them adaptable for various mechanical applications. Modular assembly options enable easy integration, reducing installation complexity. Advanced mounting systems, including crimped, bead ring, and bolted designs, offer versatile installation choices. These custom features ensure optimal performance, improving efficiency and longevity. Flexible adaptation makes next-gen air bellows ideal for high-performance applications across multiple industries.
The continuous evolution of air bellow materials is driving unprecedented performance enhancements. By leveraging advanced elastomers, high-strength reinforcements, and innovative metal alloys, modern air springs provide unparalleled durability, efficiency, and adaptability across multiple industries. As demand for high-performance suspension and isolation solutions grows, next-gen air bellows will play a crucial role in industrial and vehicular applications.