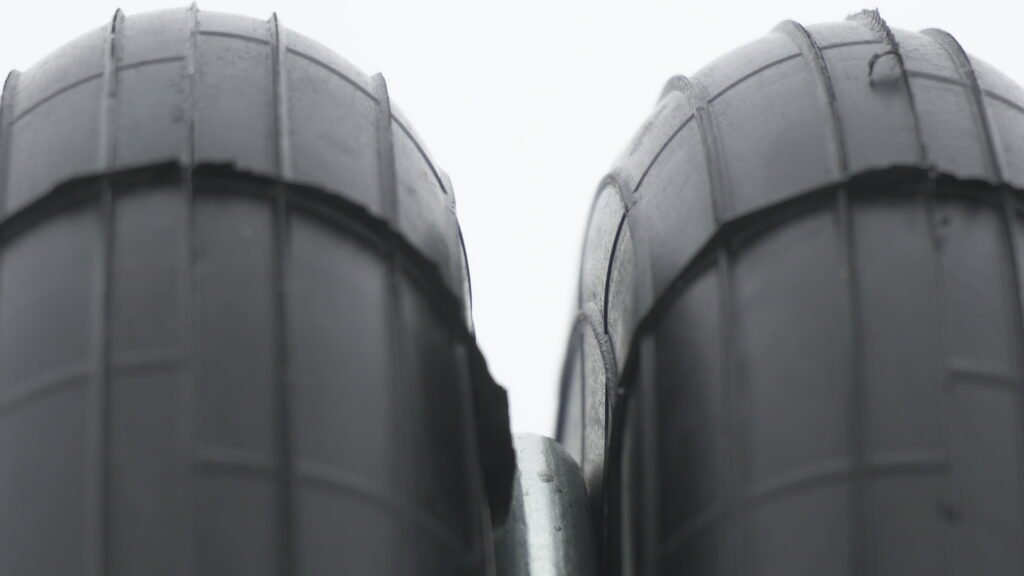
Air bellows play a crucial role in vibration isolation, actuation, and load handling. The durability of air bellows depends significantly on the elastomers used. The right elastomeric materials improve resistance to wear, temperature variations, and chemicals, extending product lifespan. Selecting the best elastomer enhances mechanical performance and reduces maintenance costs.
The durability of air bellows is determined by material resilience, external conditions, and operational cycles. Understanding these factors allows engineers to make informed choices about elastomer selection. Every industry faces different operational challenges, so a tailored approach is essential. Modern elastomer compounds offer enhanced performance under harsh conditions, making them crucial for demanding applications.
In this article, we explore the elastomers used in air bellows and their influence on durability. Understanding these materials enables companies to improve efficiency, safety, and longevity in their air spring systems.
The Importance of Elastomers in Air Bellows Performance
The performance of air bellows depends on several key properties of elastomers, such as elasticity, fatigue resistance, and chemical stability. These properties determine the ability of the air spring to maintain structural integrity under repeated load cycles.
The right elastomer ensures that the air bellows can withstand extreme pressure variations and mechanical stress. The longevity of an air bellow depends on the balance between flexibility and strength. The right compound mix minimizes failure risks and reduces long-term operational costs.
Engineers evaluate wear resistance, load endurance, and flexibility before selecting an elastomer. Advanced testing methods ensure the best-performing compounds are used. Improvements in rubber formulation continue to enhance the service life of air springs.
In industrial environments, air bellows operate under extreme vibrations and temperatures. Using high-performance elastomers guarantees efficiency and reduces downtime. Proper selection extends product reliability and ensures safe operations.
Key Properties of Elastomers for Air Bellows
To achieve maximum durability, elastomers used in air bellows must possess several critical properties. Each property contributes to performance, safety, and longevity. Here are the most essential ones:
- Flexibility and Elasticity – Allows air bellows to compress and expand effectively under varying loads.
- Abrasion Resistance – Prevents wear caused by constant friction and movement.
- Weather and Ozone Resistance – Ensures longevity in outdoor environments where exposure is unavoidable.
- Chemical Compatibility – Protects against oils, fuels, and industrial chemicals, reducing degradation risks.
- Temperature Stability – Maintains functionality in extreme heat or cold conditions.
The combination of these properties defines the performance efficiency of air springs. Engineers must carefully consider application-specific factors when choosing elastomers. A tailored elastomer formulation significantly impacts air bellows longevity.
Common Elastomers Used in Air Bellows
Different elastomer compounds are used in manufacturing air bellows, each offering specific advantages. Selecting the right material depends on the operating environment and performance requirements.
1. Natural Rubber (NR/SBR Blend)
This widely used elastomer provides excellent elasticity and dynamic properties. It is favored for applications requiring high fatigue resistance.
- Superior flexibility allows effective load absorption.
- Good abrasion resistance extends lifespan under continuous movement.
- Temperature range: -40°C to +70°C.
2. Chlorobutyl (CIIR)
Chlorobutyl is known for its outstanding chemical and heat resistance, making it ideal for demanding applications.
- Excellent acid resistance, ideal for industrial chemical exposure.
- Superior gas impermeability, ensuring constant air pressure retention.
- Temperature range: -30°C to +115°C.
3. Nitrile Rubber (NBR)
NBR is used where oil and fuel resistance are critical factors.
- Strong resistance to hydrocarbons, including diesel and lubricants.
- Excellent durability against outdoor exposure.
- Temperature range: -25°C to +110°C.
4. Ethylene Propylene Diene Monomer (EPDM)
EPDM is best suited for high-temperature and ozone-rich environments.
- High resistance to UV and weathering.
- Effective performance in steam applications.
- Temperature range: -20°C to +115°C.
5. Chloroprene Rubber (CR)
Commonly known as Neoprene, CR balances oil resistance and weather stability.
- Moderate resistance to oils and industrial fluids.
- Reliable resistance against aging and ozone exposure.
- Temperature range: -20°C to +110°C.
Impact of Elastomer Selection on Air Bellow Longevity
Selecting the correct elastomer is critical for maximizing air bellow durability. Using the wrong material can lead to premature failures due to ozone cracking, chemical degradation, or stiffness issues.
Factors Affecting Elastomer Longevity
- Load and Pressure Cycles: High-frequency movements require fatigue-resistant materials.
- Environmental Exposure: UV rays, ozone, and extreme temperatures affect material integrity.
- Contact with Chemicals and Oils: The elastomer must resist chemical attack.
- Mechanical Stress: Continuous friction and flexing accelerate wear over time.
Innovations in Elastomer Formulations for Air Bellows
Advancements in elastomer science have led to stronger and more durable materials. Modern developments include:
- Multi-layer structures, improving flexibility and durability.
- Reinforced fiber plies, enhancing structural integrity.
- Eco-friendly materials, reducing environmental impact.
- New polymer blends, improving resilience and chemical resistance.
Choosing the right elastomer is essential for ensuring air bellow efficiency, longevity, and safety. Every elastomer type offers unique benefits, making material selection crucial for specific applications. By leveraging advanced elastomer formulations, manufacturers enhance air spring durability, optimize performance, and reduce maintenance costs.