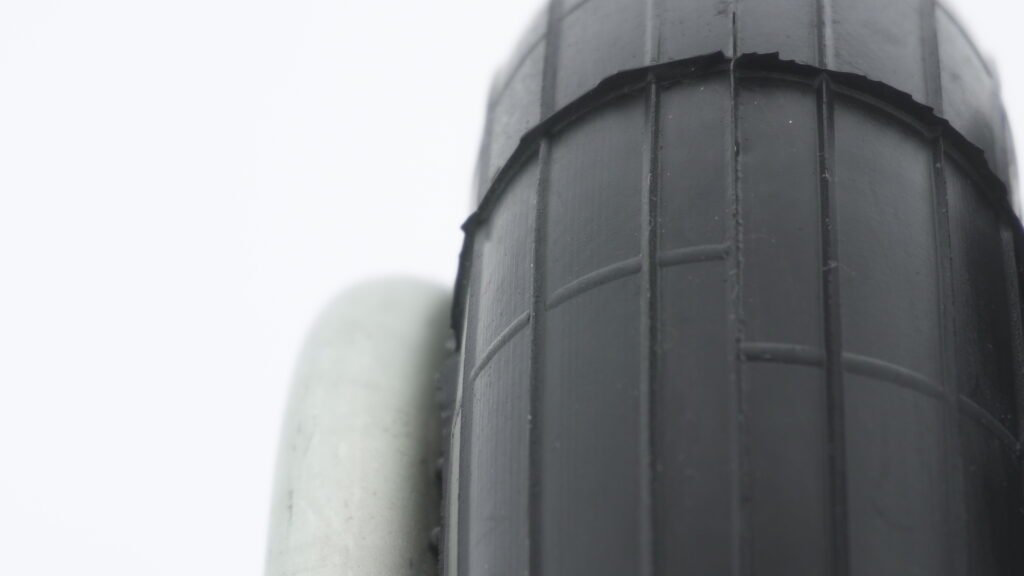
Understanding the Challenges of Harsh Environments
In industries that rely on air bellows, exposure to extreme temperatures, moisture, chemicals, and mechanical stress can severely impact performance and durability. Industrial air springs operate in demanding conditions such as manufacturing plants, transportation systems, and heavy machinery applications. Without proper maintenance and protective measures, air actuators deteriorate prematurely, leading to costly replacements and downtime. It is crucial to take preventative actions to mitigate these risks.
Choosing the Right Material for Durability
Material selection plays a critical role in extending air bellow lifespan. The choice of rubber compounds and metal reinforcements directly influences resistance to environmental stressors. Common elastomer options include:
- Natural Rubber (NR/SBR) – Provides high flexibility and wear resistance.
- Chlorobutyl (CIIR) – Offers excellent resistance to acids and heat.
- Nitrile Rubber (NBR) – Superior oil, fuel, and weather resistance.
- Ethylene Propylene Diene (EPDM) – Best suited for high-temperature applications.
- Chloroprene (CR) – Good compromise between oil resistance and durability.
For metal components, stainless steel (AISI-304/316L) is preferable due to its superior corrosion resistance compared to galvanized steel. This helps in extending the functional lifespan of the bellows under extreme conditions.
Ensuring Proper Installation for Maximum Efficiency
Improper installation is one of the leading causes of air spring failure. When setting up air bellows, follow these critical guidelines:
- Ensure correct mounting alignment to prevent uneven stress distribution.
- Use the specified torque values when tightening fasteners.
- Avoid overinflation and underinflation, which can cause premature fatigue.
- Maintain adequate clearance to prevent excessive contact with surrounding components.
By following these steps, the risk of premature wear and failure can be significantly reduced, ensuring that the air bellows operate efficiently over time.
Maintaining Optimal Operating Conditions
To increase the lifespan of air bellows, operating conditions must remain within recommended limits:
- Maintain an optimal pressure range (typically 6-8 bar for standard bellows, up to 12 bar for reinforced designs).
- Use filtered, dry air to prevent moisture accumulation and internal corrosion.
- Regularly check for external contamination, such as dirt, oil, and chemicals.
- Avoid temperature extremes, ensuring the elastomer remains within its designed range.
Keeping the operating environment controlled and free from external stressors helps improve the durability and performance of air bellows.
Implementing Preventive Maintenance Practices
A well-structured preventive maintenance plan helps detect issues before they cause failures. Key steps include:
- Routine Inspections: Conduct visual checks for cracks, leaks, or deformations.
- Leak Detection: Use a soapy water test to identify air leaks around fittings.
- Pressure Monitoring: Regularly verify that the air system operates within specifications.
- Lubrication and Cleaning: Keep all mounting hardware free from corrosion and debris.
- Replacement Scheduling: Plan predictive maintenance based on historical wear patterns.
Implementing these preventive maintenance steps significantly reduces the likelihood of unexpected failures and extends the lifespan of air bellows.
Protecting Air Bellows from Environmental Hazards
External environmental factors significantly influence air bellow longevity. Protective strategies include:
- UV Protection: Use protective coatings or covers to prevent rubber degradation from sunlight.
- Chemical Resistance: Apply special coatings or select resistant elastomers for chemical exposure.
- Abrasion Shielding: Install guard plates to shield against mechanical impact and debris.
- Thermal Insulation: Use heat shields or ensure adequate airflow in high-temperature environments.
Implementing these protection measures will help maintain the structural integrity and function of air bellows in harsh environments.
Optimizing Load Distribution
Uneven load distribution accelerates air spring wear. To achieve optimal load balance:
- Use multiple air bellows when necessary to evenly distribute force.
- Ensure proper load alignment to minimize side forces.
- Adjust the air pressure dynamically to compensate for varying loads.
- Incorporate height control systems to maintain consistent operating height.
Evenly distributing mechanical loads ensures that air bellows wear evenly and last longer.
Selecting the Right Design for Your Application
Different air bellow designs are suited for specific applications:
- Single Convolution – Compact, high-durability solution for low-stroke applications.
- Double Convolution – Balances stroke length with increased load capacity.
- Triple Convolution – Ideal for high-stroke applications with heavy loads.
- Crimped vs. Bead Ring Designs – Choose based on ease of maintenance and installation flexibility.
Choosing the right air bellow design ensures that the equipment operates efficiently while minimizing wear.
Common Signs of Air Bellow Wear and When to Replace
Recognizing early warning signs helps prevent catastrophic failures:
- Surface Cracks: Indicate rubber fatigue from environmental exposure.
- Leakage: Can be caused by punctures, degraded seals, or improper installation.
- Deformation or Bulging: Suggests internal damage or incorrect air pressure.
- Inconsistent Performance: Fluctuating load responses may indicate internal wear.
- Corrosion on Metal Components: Weakens structural integrity and connection points.
If any of these signs appear, immediate action should be taken to replace the damaged air bellows.
Proper selection, installation, and maintenance significantly extend the lifespan of air bellows in harsh conditions. By using high-quality materials, ensuring optimal operating conditions, and implementing a rigorous maintenance strategy, industries can maximize efficiency while reducing operational costs. Regular inspections, environmental protection, and load optimization further contribute to prolonged service life. Implement these strategies today to enhance the durability and reliability of your air bellows.