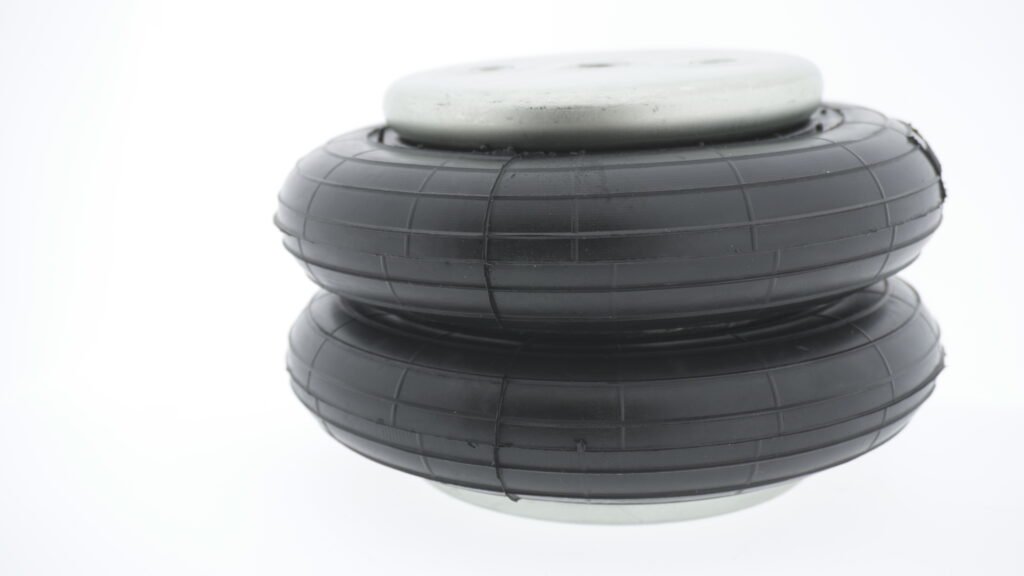
The food processing industry faces constant demands for efficiency, precision, and hygiene compliance in its operations. These industries need advanced technologies to ensure productivity and meet strict safety regulations. Air bellows have become essential in addressing these challenges. They enhance vibration isolation, improve machinery lifespan, and ensure smoother processes. With more than 99% vibration reduction, air bellows also reduce noise pollution, creating better work environments.
Key Benefits of Air Bellows
- Reduced vibration: Ensures smoother operations and increased precision.
- Noise reduction: Improves workplace environment.
- Extended machinery life: Minimizes wear and tear.
These features make air bellows indispensable for modern food production, supporting equipment like mixers, packaging systems, and conveyors. By minimizing wear and tear, air bellows significantly lower maintenance costs. Their adaptability to changing loads ensures accuracy in processes handling delicate products, such as bakery items and beverages.
Enhanced Vibration Isolation for Delicate Processes
Air bellows are a cornerstone of vibration isolation in the food industry, helping machinery operate with precision and reducing errors. Machinery vibrations often compromise efficiency, damaging sensitive components over time. Air bellows, with their unique properties, eliminate such disturbances. They stabilize machinery, especially vital for weighing and filling processes requiring utmost accuracy. Vibrations also contribute to inefficiencies and noise pollution. Air bellows counteract these issues with their low natural frequency, ensuring uniform product handling and quality. Particularly in bakeries, air bellows preserve delicate textures during dough handling. For systems like mixers, they enhance durability by absorbing operational shocks. Compact and adaptable designs further support food processing, making air bellows invaluable for minimizing disturbances and boosting performance. Their versatility in adapting to dynamic environments is a key reason for their widespread use. This stability leads to longer machinery life, ensuring cost-efficiency across production lines.
Compact and Hygienic Design for Food Safety
Food processing demands both compact equipment and adherence to stringent hygiene standards. Air bellows, designed for efficient integration, meet these requirements perfectly. Their low-profile construction ensures seamless incorporation into existing setups, even in limited spaces. Hygienic materials, such as chlorobutyl rubber and stainless steel (AISI-304 or AISI-316L), enhance durability and resist acids or cleaning agents. These properties are critical in handling applications like meat processing or beverage manufacturing. Moreover, they maintain performance under high temperatures and rigorous sanitation processes, ensuring compliance with global standards. Their maintenance-free nature further supports hygienic operation, eliminating concerns over contamination risks. By combining compact design and material integrity, air bellows enable manufacturers to optimize processes while meeting health and safety benchmarks. Their extended service life minimizes replacements, contributing to lower long-term costs. This dual focus on hygiene and efficiency solidifies air bellows’ position as essential tools for modern food production systems.
Efficient Height and Load Adjustment
Dynamic production environments require adaptable systems, and air bellows excel in height and load adjustments. These components automatically adapt to changing loads, maintaining consistent height and performance levels. Conveyors, for instance, benefit from uniform height control, ensuring smooth operation regardless of varying product weights. Similarly, packaging lines use air bellows to ensure precision during sealing or labeling processes. This adaptability minimizes manual adjustments, streamlining workflows. Additionally, load distribution capabilities of air bellows reduce strain on components, prolonging machinery lifespan. In poultry processing lines, they handle weight fluctuations effectively, contributing to operational efficiency. Uniform performance, even under variable conditions, ensures reliability. By preventing uneven wear, air bellows reduce maintenance demands. Their ability to support diverse equipment configurations makes them ideal for industries prioritizing flexibility and efficiency. Through enhanced adaptability and low-maintenance operation, air bellows improve productivity and reduce long-term costs.
Cost-Effective Solutions with Long Service Life
Compared to traditional actuators, air bellows provide cost-efficient, long-lasting alternatives for the food processing industry. Unlike pneumatic cylinders, air bellows have no sliding seals, reducing wear and maintenance needs. Their flexibility allows lateral misalignment absorption, eliminating precision guide requirements. Compact designs further save space, enabling streamlined equipment layouts. These advantages collectively lower operational expenses, optimizing production economics. Moreover, the durable construction of air bellows withstands exposure to harsh environments, maintaining performance under extreme temperatures and chemicals. Their robust design eliminates frequent replacements, ensuring higher reliability across machinery. These cost-saving properties position air bellows as superior to conventional solutions. Their extended service life reduces disruptions, keeping production lines operational longer. Additionally, their simplicity minimizes training or troubleshooting costs. These qualities make air bellows the preferred choice for plants focusing on cost control and operational stability. Their benefits extend beyond savings, ensuring efficient and effective systems in demanding environments.
Applications in Automation and Robotics
Automation dominates modern food processing, and air bellows form an integral part of robotic systems. These components offer unique properties, such as uniform movement and angular tilt capabilities, enabling robotic arms to handle complex tasks with precision. Pick-and-place robots, for example, rely on air bellows to manage varying product shapes and sizes efficiently. In filling machines, air bellows allow precise vertical motion for accurate liquid or powder dispensing. Their ability to absorb vibrations ensures smooth operation, reducing system errors. Additionally, high load-bearing capacity makes them suitable for palletizing or material handling tasks. Automation systems benefit from their compactness, integrating easily into preexisting designs. The adaptability of air bellows enhances robotic system efficiency, supporting high-speed production lines. Their robustness reduces wear during intensive operations, ensuring reliability. Through their seamless integration and advanced performance, air bellows significantly improve automation’s scope, delivering reliability and precision crucial for food industry robotics.
Tailored Designs for Industry Needs
Air bellows cater to diverse production demands through customized designs, ensuring compatibility with specific industry needs. Available in single, double, or triple convolutions, these configurations address varying stroke lengths and force requirements. Custom options include bead ring or crimped designs, suited for machinery with unique specifications. High-pressure applications benefit from four-ply construction, increasing durability and performance. These tailored features ensure air bellows meet the exact needs of production lines, providing enhanced adaptability. For manufacturers, customization reduces the need for aftermarket adjustments, saving time and resources. Air bellows’ flexibility supports integration into advanced systems, even in niche applications. By addressing specific operational challenges, these solutions improve overall process reliability. Their versatility also ensures compatibility with future upgrades, aligning with industry growth. Whether in precision packaging or bulk material handling, tailored air bellows solutions optimize productivity, making them indispensable for modern food production challenges.
Air bellows have transformed the food processing industry by delivering innovative solutions to enhance efficiency and maintain hygiene. Their impact on vibration isolation, load adaptability, and cost reduction addresses the core challenges manufacturers face. Air bellows reduce operational costs, minimize downtime, and ensure compliance with stringent safety regulations. Summary of benefits includes improved productivity, lower operational expenses, and longer machinery lifespan. By adopting air bellows, food manufacturers can achieve consistent quality and reliability across diverse applications. These tools represent a versatile, future-proof investment for plants aiming to excel in competitive markets. Through tailored designs, automation enhancements, and exceptional adaptability, air bellows continue to redefine standards in food production. Their role in modern systems highlights their necessity for any operation focused on innovation and efficiency.