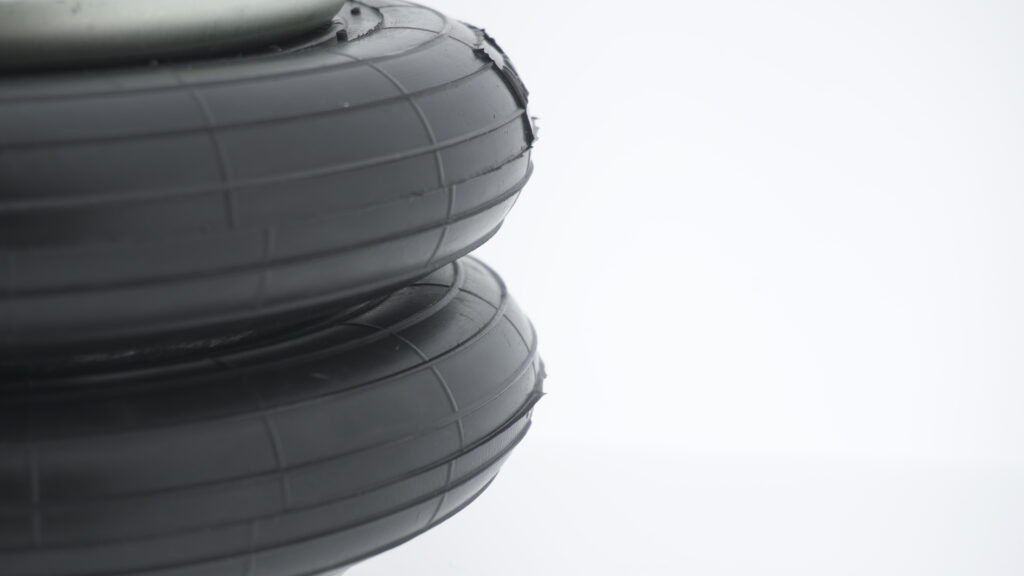
Understanding Core Components and Key Concepts
When discussing air springs, it’s critical to understand the terminology and design elements that define their operation. Air springs, often referred to as air bellows, are indispensable in both industrial actuation systems and vibration isolation solutions. With advancements in materials science and manufacturing, air springs now offer unparalleled performance across various applications.
Air springs are designed to deliver exceptional performance. Their ability to manage both motion and vibration makes them ideal for many industries. Understanding their technical elements is essential for optimal use and maintenance. Below, we break down the fundamental terms and components you should know.
Air Spring Construction
Air springs are built from a corrugated, flexible rubber body, reinforced with fabric plies and fitted with metallic end closures. This structure enables the spring to deliver a reliable axial force, ideal for applications requiring precise stroke and motion control.
The construction of air springs involves multiple layers of durable materials. These materials ensure the product’s flexibility and strength. The inner and outer rubber layers work together with reinforcement plies to withstand pressure. Steel bead plates are added to provide robust end closures. These components are vulcanized to create a reliable, long-lasting air spring.
Key Design Variations
- Crimped Design: Non-dismountable, using mechanically crimped bead plates. Ideal for high-pressure systems. This design ensures durability and simplifies installation.
- Bead Ring Design: Dismountable, with threaded or countersunk bead rings for direct assembly. This design provides flexibility for repairs.
- Dismountable Design: Uses clamping bead rings with top and bottom plates, offering flexibility for maintenance. This option is ideal for customizable systems.
These designs cater to different applications, ensuring that users can select the best option for their needs. Choosing the correct design will optimize performance and reduce maintenance requirements.
Materials Used
Air springs rely on high-quality materials for durability and performance. The choice of materials impacts their operating conditions and lifespan.
- Rubber Compounds:
- Natural Rubber (NR/SBR): Excellent dynamic properties, operating at -40°C to +70°C. Suitable for general-purpose applications.
- Chlorobutyl (CIIR): Superior resistance to acids, suitable for -30°C to +115°C. Ideal for chemical environments.
- Nitrile (NBR): Outstanding oil and ozone resistance, operating between -25°C and +110°C. Best for industrial applications.
- Metallic Parts: Available in electro-galvanized steel, AISI-304 stainless steel, or AISI-316L stainless steel for harsh environments. These materials resist corrosion and wear, ensuring longevity.
Selecting the right material is essential for matching the air spring to its operating environment. Proper materials prevent premature failure and ensure consistent performance.
Operating Media
While primarily designed for compressed air, air springs can also operate with nitrogen, water, or oil-laden compressed air. For water-based applications, corrosion-resistant metal components are essential.
The ability to handle various media makes air springs versatile. However, proper maintenance and material selection are crucial when working with alternative media. For example, water-based applications require stainless steel parts to avoid corrosion. Always consult manufacturers for specific recommendations.
Pressure and Force Handling
Standard air springs operate at 8 bar, but high-strength four-ply designs can withstand up to 12 bar, enabling greater force output.
This pressure range allows air springs to meet diverse application requirements. High-pressure systems benefit from reinforced designs, which offer enhanced safety and durability. Understanding the pressure limits is vital for safe and effective use.
Advantages of Air Springs
As Isolators
Air springs are highly effective as vibration isolators. Their design minimizes unwanted movement, protecting equipment and improving efficiency.
- Vibration Isolation: Over 99% vibration reduction. This ensures smooth operation of sensitive machinery.
- Noise Reduction: Minimizes structure-borne noise. This feature is essential for maintaining a quiet work environment.
- Height Control: Ensures consistent operating height under varying loads. This improves stability and performance.
- Compact Design: Enables use in tight spaces. This allows for flexible installation.
These features make air springs an excellent choice for isolating machinery and structures. Their ability to adapt to different loads ensures long-term reliability.
As Actuators
Air springs are also used as actuators in various industrial applications. They offer precise motion control and adaptability.
- Lateral Misalignment Compensation: Absorbs up to 30 mm misalignment. This reduces wear and extends equipment life.
- Cost Efficiency: Lower cost compared to traditional cylinders. This makes them an economical choice.
- Uniform Movement: Eliminates stick-slip effects. This ensures smooth, consistent operation.
These advantages highlight the versatility of air springs. Their unique properties make them suitable for both static and dynamic applications.
Applications in Industrial Environments
Air springs are commonly used in:
- Automotive Suspension Systems: For enhanced ride quality and load leveling. Air springs improve vehicle performance and safety.
- Industrial Actuators: For precise motion control in assembly lines. They ensure consistent output and reliability.
- Vibration Isolation Platforms: To protect sensitive equipment from external vibrations. This application extends equipment lifespan.
These applications demonstrate the wide range of uses for air springs. Their adaptability makes them a valuable tool across industries.
Maintenance Considerations
Proper storage is crucial. Rubber components must be kept away from direct sunlight, ozone-generating devices, and extreme temperatures, as per ISO 2230 guidelines.
Regular inspections and proper storage conditions extend the lifespan of air springs. Following manufacturer recommendations ensures optimal performance and minimizes downtime.
Air springs, with their diverse designs, materials, and applications, are a cornerstone of modern industrial systems. By understanding their terminology and specifications, industries can optimize performance, enhance efficiency, and reduce operational costs.
Understanding the terminology behind air springs is essential for selecting the right product. With proper knowledge, users can unlock the full potential of these versatile components.