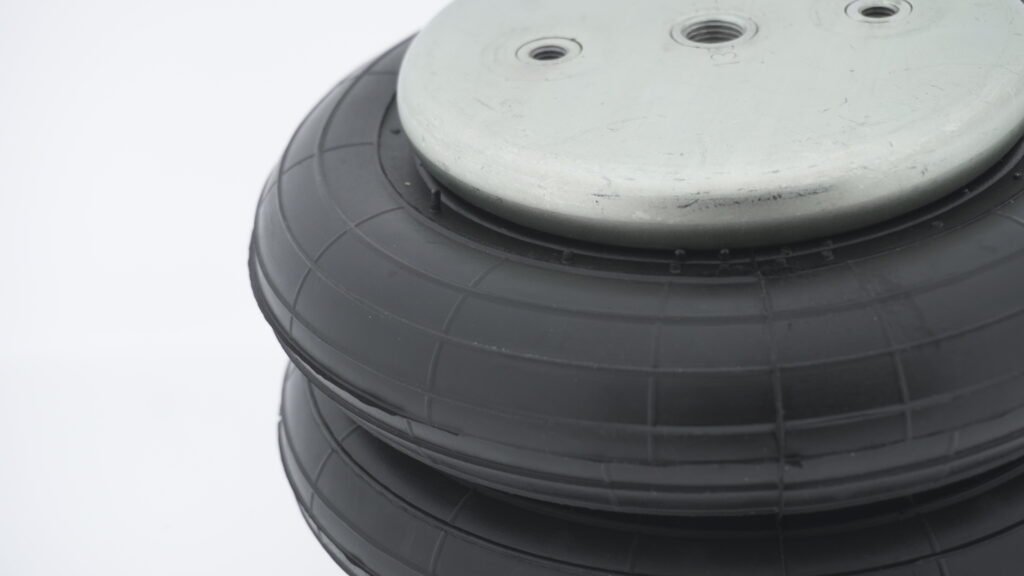
Optimizing the height of air bellows is critical for ensuring their peak performance across a range of industrial and vehicular applications. Height adjustment directly influences load management, vibration isolation, and durability. In this guide, we delve into the essentials of air bellow height adjustment and explore best practices for achieving optimal system performance. This topic is particularly important for those working in dynamic and demanding operational settings.
Why Proper Height Adjustment Matters
Adjusting the height of air bellows impacts the system’s load distribution, stroke capacity, and stability. Incorrect height settings can lead to premature wear due to overextension or compression, reduced isolation efficiency, affecting vibration damping, and safety risks in dynamic environments. Correctly calibrated air spring systems prevent such issues and enhance overall performance longevity, reducing operational downtime and maintenance costs.
Key Factors for Height Optimization
1. Operating Pressure and Load Requirements
The operating pressure should align with the specified dynamic load requirements. For example, standard models such as 6″ x 2 bellows operate optimally between 5 and 8 bar pressure, with a maximum load capacity of 2,000 daN at a static height of 150 mm and dynamic pressures reaching up to 8 bar under controlled conditions. These specifications ensure the longevity of the bellow and minimize the chances of failure during heavy-duty applications. Additionally, users should ensure the air supply system maintains consistent pressure to avoid uneven loading that could disrupt operational efficiency.
2. System Configuration and Stroke Length
Different configurations, such as single-acting and multi-convoluted bellows, exhibit varied stroke lengths and height tolerances. For instance, single-acting models typically provide stroke lengths ranging from 50 mm to 150 mm, while multi-convoluted bellows can achieve strokes of up to 400 mm, depending on the model. Height tolerances also vary, with single-convoluted models maintaining stability within ±5 mm, and multi-convoluted systems allowing adjustments up to ±15 mm for dynamic applications. These differences make it essential to select the appropriate bellow configuration based on specific application needs.
- For single-convolution models, height adjustments are minimal but provide excellent stability.
- Multi-convoluted systems, such as 10”x3 stainless steel bellows, allow extended stroke ranges for larger adjustments.
3. Angular and Axial Misalignment
Air bellows tolerate some misalignment, but exceeding the recommended angles can cause structural damage. For most models, an angular misalignment of up to 10° and an axial deviation of up to 5 mm are permissible, ensuring safe and reliable performance in dynamic environments. Misalignment risks can be mitigated by careful inspection of mounting setups and using adjustment jigs or tools during installation to maintain precise angular settings.
Step-by-Step Height Adjustment Process
Step 1: Inspect and Secure Components
Before adjustment, ensure the bellows are vented of any residual air, mounting hardware, such as end plates and bolts, is tightened to recommended torque values, and alignment brackets are correctly positioned. Proper preparation is critical to maintaining operational safety and efficiency.
Step 2: Inflate to Recommended Static Height
Inflate the bellows gradually to achieve the static height specified in the technical data sheet. Below is a reference table of static heights for common air bellow models under various pressures:
Model | Pressure (bar) | Static Height (mm) |
---|---|---|
6″x2 | 6 | 150 |
10″x3 | 6 | 200 |
12″x2 | 6 | 170 |
8″x1 Stainless | 6 | 125 |
8″x2 Stainless | 6 | 200 |
Refer to this table for quick adjustments during installation or maintenance. Achieving the proper height is essential for optimal performance and load distribution during operation.
Step 3: Adjust for Dynamic Applications
For systems involving dynamic motion, adjust the height to balance between stroke capacity and load stability. Factor in variables such as cyclic loading frequencies and stroke length variations during operation. Consistent recalibration ensures system stability even under variable operational demands.
Step 4: Final Inspection and Testing
Perform a full system check to ensure no air leaks are present, verify that the system responds effectively to load variations and vibrations, and conduct a test cycle under expected operating conditions. These steps provide assurance that the system will operate reliably under varying environmental and mechanical stresses.
Enhancing System Longevity
Proper height adjustment not only optimizes performance but also extends the life of the bellows. Regular inspections for signs of wear or fatigue, particularly at connection points, maintaining proper air quality by adhering to ISO 8573 standards, and replacing worn components promptly can significantly enhance system durability.
Common Challenges and Solutions
Overinflation
Overinflation reduces flexibility and increases stress on the material. Always monitor pressure using calibrated gauges and adhere to manufacturer-recommended maximum pressures (e.g., 8 bar for standard models). Regular maintenance of pressure monitoring systems can help prevent this issue.
Misalignment Issues
Misalignment leads to uneven load distribution and premature wear. Use alignment tools and ensure the mounting surface is level to mitigate risks of misalignment. Precise installation practices reduce operational downtimes due to misalignment corrections.
Environmental Factors
Extreme temperatures or exposure to corrosive substances can degrade performance. Standard air bellows typically operate within a temperature range of -30°C to +70°C, while high-temperature models can withstand up to +115°C. For corrosive environments, stainless steel components and rubber compounds resistant to oils and chemicals provide enhanced durability and compatibility. These features make them ideal for demanding industrial applications.
Optimizing the height of air bellows is an essential step in ensuring their performance, safety, and longevity. By understanding the technical parameters and adhering to best practices, we can achieve maximum efficiency in applications ranging from industrial vibration isolation to vehicle suspension systems. Regular inspection, precise adjustments, and adherence to manufacturer specifications will lead to reliable and consistent system operation.