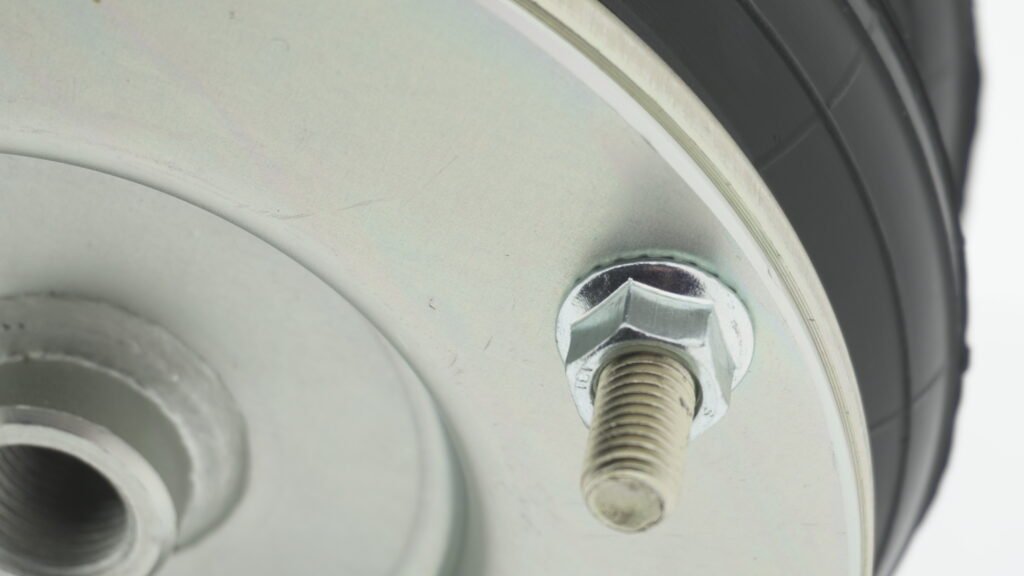
In our industry, the environmental impact of our products is a critical consideration. As engineers specializing in air bellows, we understand the importance of evaluating the sustainability of our solutions. This article delves into the environmental aspects of air bellows, examining their production, usage, and end-of-life disposal.
Production Process and Materials
The production of air bellows involves several materials, primarily rubber and metal components. The rubber compounds used in air bellows, such as Natural Rubber (NR/SBR), Clorobutyl (CIIR), Nitrile (NBR), Ethylene Propylene Diene (EPDM), and Chloroprene (CR), each have different environmental footprints. For instance, Natural Rubber is derived from latex, a renewable resource, but its cultivation can impact biodiversity. On the other hand, synthetic rubbers like Nitrile and EPDM are petroleum-based, which raises concerns about fossil fuel consumption and greenhouse gas emissions.
The metal components, typically made from electro-galvanized steel or stainless steel (AISI-304, AISI-316L), also have environmental implications. The extraction and processing of these metals are energy-intensive and can result in significant carbon emissions. However, the durability and recyclability of these metals can mitigate some of these impacts.
Usage and Efficiency
Air bellows are designed to work with compressed air, but they can also operate with nitrogen, oil, water, and compressed air containing oil. The choice of working media can influence the environmental impact. For example, using compressed air is generally cleaner compared to oil, which can pose risks of leaks and spills.
One of the key environmental benefits of air bellows is their ability to improve the efficiency of machinery by providing superior vibration isolation and load distribution. This can lead to reduced wear and tear on equipment, lower maintenance requirements, and extended machinery lifespan, all of which contribute to a lower environmental footprint.
Maintenance and Longevity
Proper maintenance of air bellows is crucial for maximizing their lifespan and minimizing environmental impact. Regular cleaning with water, soap, or alcohol (methyl, ethyl, or isopropyl) is recommended to prevent damage from aggressive substances and rusting of metal parts. Avoiding the use of abrasives, organic solvents, and direct pressurized steam cleaning systems is essential to maintain the integrity of the rubber bellows.
Routine inspection of the rubber bellows and pneumatic components, such as valves, air pipes, and regulators, helps identify and address potential issues before they lead to failure. Ensuring tight connections and proper storage conditions (cool, dark, and dry environments) also contributes to the longevity of air bellows.
End-of-Life Disposal
The disposal of air bellows at the end of their life cycle presents environmental challenges. Rubber components are not biodegradable and can persist in the environment for long periods. However, recycling options are available for both rubber and metal parts. For instance, rubber can be repurposed into products like playground surfaces and athletic tracks, while metals can be melted down and reused in new products.
In conclusion, while air bellows have certain environmental impacts associated with their production and disposal, their benefits in terms of efficiency, durability, and maintenance can offset some of these concerns. By choosing the right materials, maintaining the equipment properly, and exploring recycling options, we can enhance the sustainability of air bellows.